مراحل ساخت اسکلت فلزی
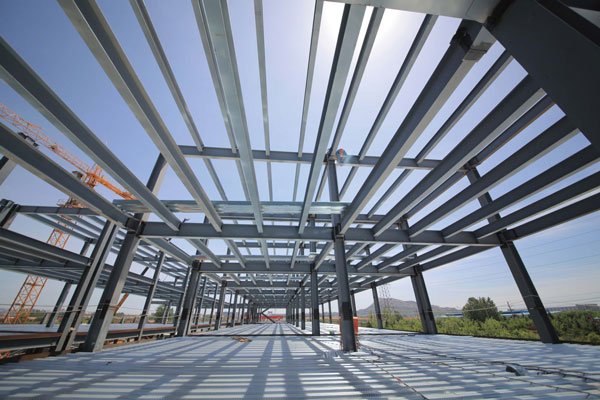
در حال حاضر، ساخت ساختمان و سوله ها در ایران، به دو روش اسکلت فلزی و اسکلت بتنی صورت می گیرد. انتخاب بین این دو روش، به عوامل متعددی بستگی دارد که از جمله آن ها می توان به شرایط آب وهوایی منطقه، میزان بودجه موجود، کیفیت و شرایط اجرا و مسائل فنی سازه اشاره کرد؛ اما در یک مقایسه کلی، اسکلت فلزی که گاهی به آن اسکلت فولادی نیز میگویند، به دلیل مزایای فراوان خود نسبت به اسکلت بتنی، محبوبیت وکاربرد فراوانی یافته است. اسکلت فلزی، از شبکه ای منظم از تیرها و ستون ها تشکیل شده است که به صورت عمودی و افقی در کنار هم قرار گرفته و با رعایت استانداردهای مشخصی طراحی و نصب می شوند. استفاده از این اسکلت به دلیل ایجاد استحکام و مقاومت بالا، یکی از بهترین گزینه ها برای ساخت اسکلت انواع سازه ها به شمار می رود. در ادامه، به بررسی مزایای اسکلت فلزی به صورت دقیق تری پرداخته و مراحل ساخت و اجرای آن را نیز شرح خواهیم داد.
ساخت اسکلت فلزی چه مزایایی دارد؟
سرعت اجرای اسکلت
یکی از بزرگ ترین مزایای اسکلت فلزی، سرعت بالای اجرای آن است. همزمان با تخریب سازه قدیمی و آغاز گودبرداری، شرایط ساخت اسکلت فلزی در کارخانه نیز فراهم می گردد. این امر، باعث افزایش سرعت در اتمام پروژه ها، کاهش هزینه های زمانی و در نتیجه، افزایش بازدهی مالی خواهدشد.
سادگی نصب در محل
از آن جایی که بیشتر عملیات ساخت اسکلت فلزی در کارخانه انجام می شود، نصب آن در محل، بسیار ساده تر از اسکلت بتنی است. این روش، نه تنها زمان اجرای پروژه را کاهش می دهد، بلکه کنترل کیفیت را نیز با استانداردهای بالاتری ممکن می سازد.
بازدهی بیشتر
همانطور که گفتیم، مدت زمان اجرای اسکلت فلزی، کم تر از اسکلت بتنی است و همین امر، باعث اتمام سریع تر پروژه و کاهش هزینه های سربار می شود. همچنین، ابعاد ستون های فلزی، به مراتب کم تر از ستون های بتنی است که وجود این مسئله، منجربه افزایش زیربنای مفید برای ساختمان، بهبودکیفیت فضاهای معماری و داخلی و مطلوب سازی هرچه بیشتر آن برای برای مصرف کننده نهایی خواهد شد.
مراحل تولید و ساخت اسکلت فلزی در کارخانه
تولید و ساخت اسکلت فلزی در کارخانه، شامل مراحل تخصصی و متعددی است که برای تضمین کیفیت و دقت در اجرای پروژه ها، باید بهصورت دقیق و منظم انجام شوند. در ادامه، هر یک از مراحل تولید و ساخت این اسکلت، به صورت مفصل بررسی خواهندشد:
برنامه ریزی تولید
زمان بندی و برنامه ریزی دقیق، یکی از اصول اساسی در هر پروژه ای است. به منظور دستیابی به محصول باکیفیت در بازه زمانی مشخص، برنامه ریزی زمانی دقیق الزامی است. پس از تهیه نقشه های کارگاهی و تعیین لیست قطعات، واحد برنامه ریزی تولید، با توجه به اهمیت و نوع هر قطعه، برنامه تولید را تدوین و به خط تولید ابلاغ می کند. این برنامه، شامل زمان بندی مراحل مختلف تولید بوده و باید به صورت منظم اجرایی شود تا از تأخیرها و مشکلات احتمالی جلوگیری کند.
قطعه زنی
این مرحله، شامل فرآیندهایی نظیر باز کردن رول ها (در صورت نیاز)، تمیزکاری ورق، برش کاری، سوراخ کاری و پخ زنی است. ورق های خریداری شده، ممکن است سطحی روغنی و زنگ زده داشته باشند که در این صورت باید تمیز شوند تا کیفیت جوشکاری بهبود یابد. در کارگاه های سنتی، قطعه زنی بر اساس جدول های اکسل انجام می شود؛ اما در کارخانه های مدرن، این عملیات بر اساس نقشه های تکلا استراکچر صورت می گیرد. مرحله قطعه زنی، باید جلوتر از مونتاژ اولیه باشد تا مونتاژکاران بدون تأخیر کار کنند. در صورت خرابی دستگاههای برش نیز، باید قطعات کافی برای مونتاژ موجود باشد تا عملیات به تعویق نیفتد.
تمیزکاری و سندبلاست اولیه
مواد خام، پیش از ورود به سالن قطعه زنی، تمیزکاری (زنگ زدایی) می شوند. این عملیات، شامل سندبلاست، اسیدشویی و استفاده از برس های سیمی است که به دلیل افزایش کیفیت جوش قطعات انجام می شود. تمیزکاری دقیق سطح ورق ها، از اهمیت ویژه ای برخوردار است؛ زیرا وجود هر گونه آلودگی، کیفیت جوش را کاهش داده و منجر به ضعف ساختاری در سازه می شود.
برش کاری و پخ زنی
برش ورق ها، توسط گیوتین هیدرولیکی و دستگاه های CO2 برش، هوابرش و پلاسما انجام می شود. همچنین، برش کاری پروفیل هایی مانند میلگرد، نبشی و تیرآهن نیز، توسط دستگاه های اره لنگ و اره آتشی صورت می گیرد. پس از اتمام برش های اصلی، به دستگاه برش حرارتی زاویه داده شده و پخ لازم برای انجام جوش شیاری، به لبه ها داده می شود. این مرحله، برای تضمین اتصالات قوی و مطمئن بین قطعات، حیاتی است.
تسمه سازی و بازرسی جوش درزها
تسمه سازی، برای اجزای ساخته شده از ورق به کار می رود. ورق ها، معمولاً به طول 6 متر در بازار موجود بوده و برای ساخت اعضای بلندتر مانند ستون ها و شاه تیرها، تسمه سازی ضروری است. ورق ها، باید صاف و بدون پیچیدگی باشند تا مونتاژ صحیحی صورت گیرد. در مرحله مونتاژ، تسمه ها بر روی یک شاسی مسطح و در راستای صفحات عمودی کوچک (لچکی) قرار گرفته، درزجوش ها هم راستا شده و با خال جوش به یکدیگر متصل می شوند. قطعاتی که با جوش شیاری و به صورت لب به لب به یکدیگر متصل می شوند، باید هم باد یکدیگر قرار گرفته و به وسیله پیچ، گیره، گوه، قید یا خال جوش، تا اتمام جوشکاری تثبیت شوند. در این مرحله، سوراخ کاری بسته به نوع و ضخامت قطعه، به دو روش پانچ و دریل انجام می شود.
مونتاژ و جوش مقاطع
در این مرحله، قطعات پس از عملیات تسمه سازی و سوراخ کاری، جهت مونتاژ اولیه، مونتاژ بال و جان و خال جوش کردن، در داخل قالب ها ثابت شده و به روش جوشکاری زیر پودری جوش داده می شوند. این نوع جوشکاری، مزایایی چون نفوذ کامل، یکنواختی سطح جوش، عدم ایجاد تابیدگی، سرعت بالا و کیفیت بهتری دارد. به عنوان مثال، در ساخت یک ستون، ابتدا بدنه اصلی ستون و دستک ها بهصورت مجزا در قالب های مخصوص مونتاژ شده و سپس، ورق های بال و جان ستون، جوشکاری می شوند. اگر طول ستون بیش از 6 متر باشد، ورق های بعدی به صورت ریسمانی در امتداد یکدیگر قرار می گیرند. باتوجه به تثبیت قطعات در این مرحله، جلوگیری از هرگونه جابجایی و عدم تطابق، بسیار حائز اهمیت است.
ساخت قطعات فرعی
آخرین مورد، ساخت قطعات فرعی است. همزمان با ساخت قطعات اصلی، قطعات فرعی مانند ورق بادبند، دستک طره ها و سایر اجزای مشابه نیز ساخته شده و مانند قطعات اصلی، تمیزکاری، برش کاری، سوراخ کاری و مونتاژ نهایی می گردند. قطعات فرعی، نقش مهمی در استحکام و پایداری سازه داشته و باید با دقت و طبق استانداردهای مربوطه تولید شوند.